...the broken ball end of a 2mm hex wrench from a screw?
While reinstalling a screw that holds the optics plate in place on my S&W M&P .22Mag pistol the ball end of the hex wrench broke off in the screw head. It didn't quite break off flush with the screw head, but pretty close. And it's only 2mm.
I've tried a few things to get it out but it's just too small and it's too tightly in place to get anything to grab it or pry it out. I'm thinking my only option is to maybe drill it out. But that's gonna be really tricky. I'm not even sure I have a drill bit in the 1.5mm range. That's pretty tiny.
Any suggestions? Or is drilling it the only way.

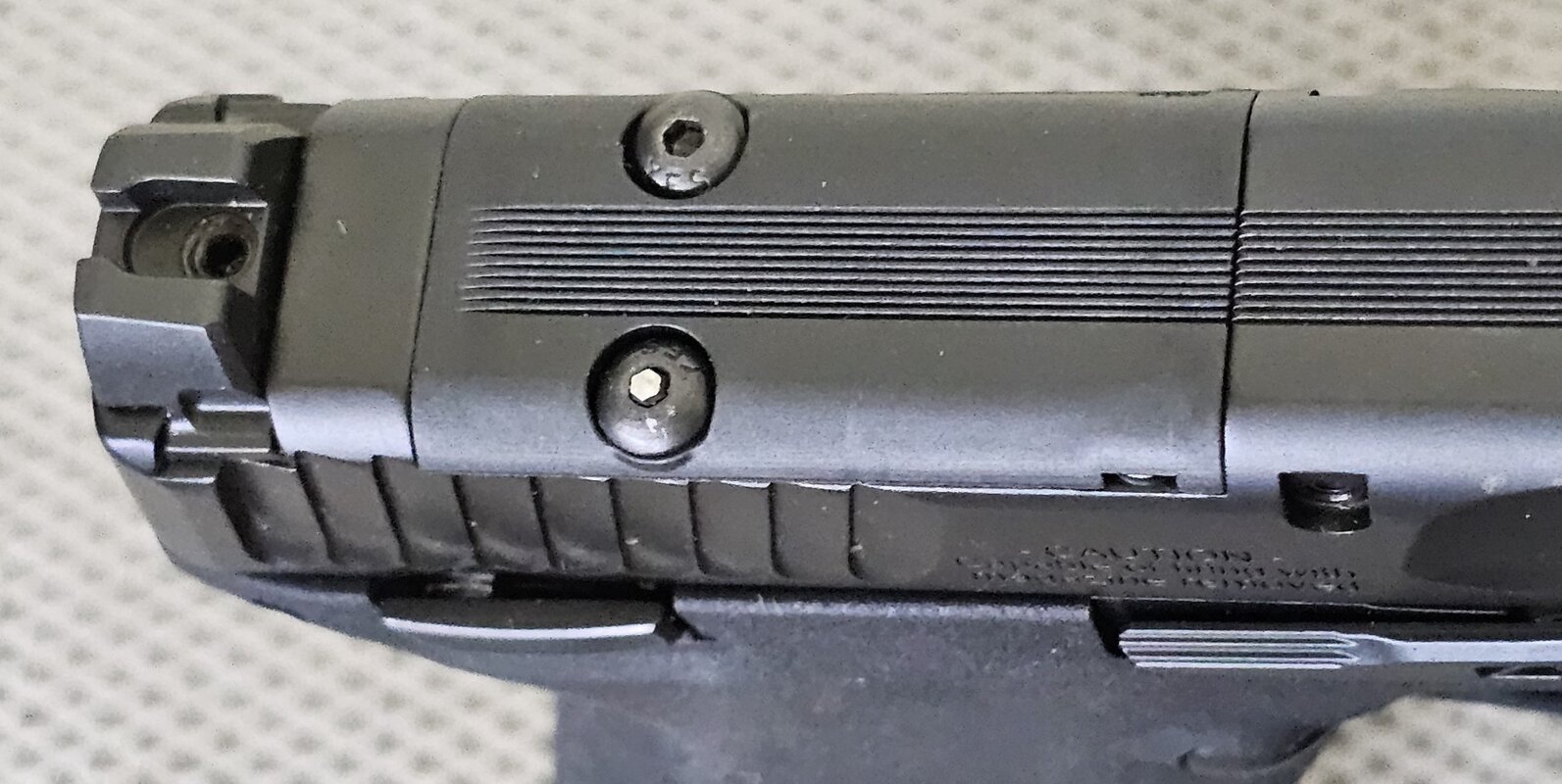
While reinstalling a screw that holds the optics plate in place on my S&W M&P .22Mag pistol the ball end of the hex wrench broke off in the screw head. It didn't quite break off flush with the screw head, but pretty close. And it's only 2mm.
I've tried a few things to get it out but it's just too small and it's too tightly in place to get anything to grab it or pry it out. I'm thinking my only option is to maybe drill it out. But that's gonna be really tricky. I'm not even sure I have a drill bit in the 1.5mm range. That's pretty tiny.
Any suggestions? Or is drilling it the only way.

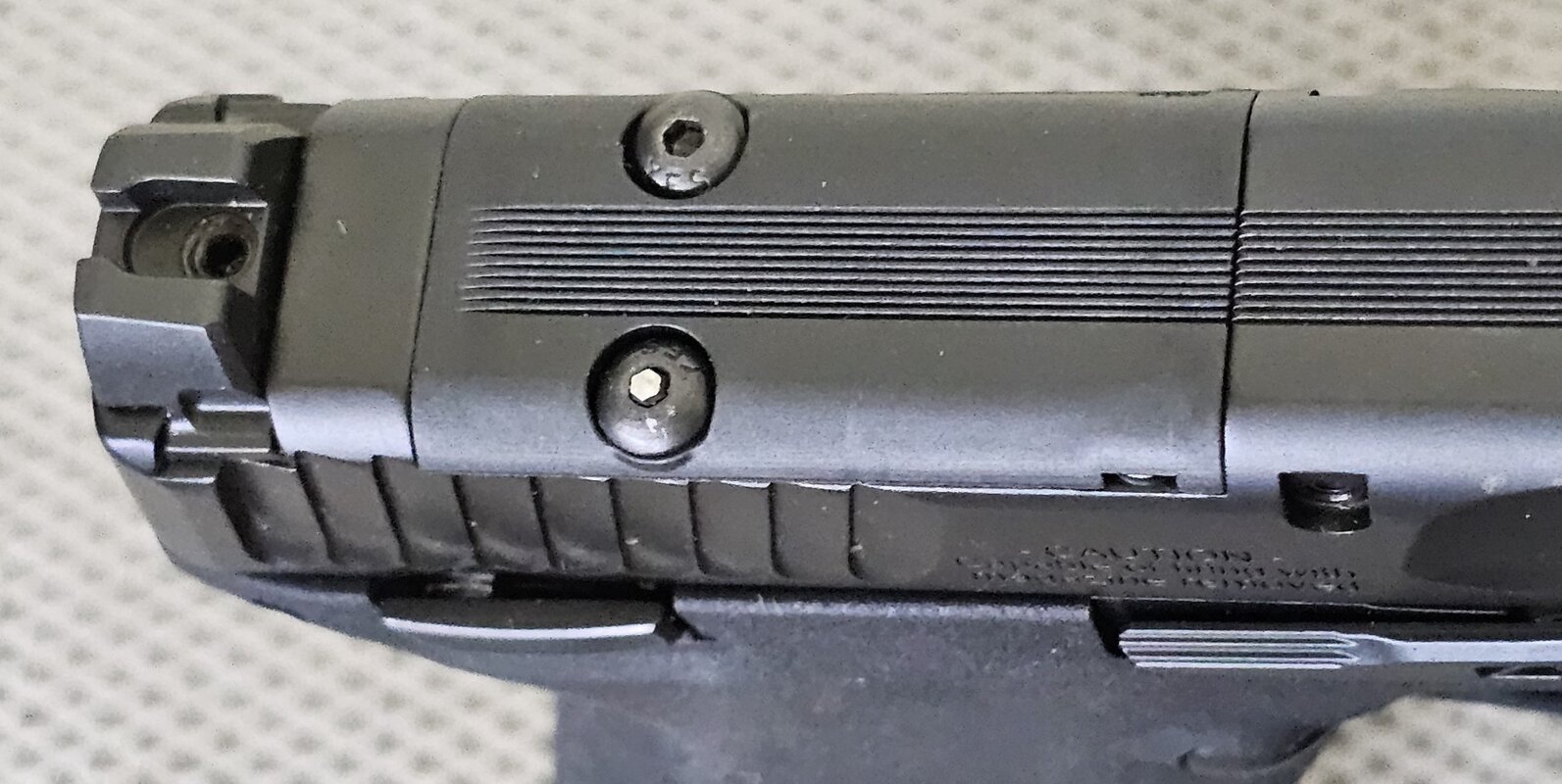